used in mining use powder concentrator air inlet and air outlet rubber lining pipeline repairing and protecting
The wind speed of the shell of air inlet/outlet and choosing powder area periphery part is very high (18 to 30 m/s),a large number of dust based on
airflow entrainment high-speed scour shell to cause the wind erosion abrasion.Using the method of sticking high hardness wear resistant ceramic
tile to do the abrasion proof processing,the theory life can reach more than 10 years.But because the shell shape is irregular,it's easy to appear local
falling off for sticking the fixed abrasion resistant ceramic tile,so we requires that the using wear resistant ceramic adhesive has very high
bonding strength.
Xiangyang City Hundred Shield Coating Material Co.,Ltd devotes itself to the research & development and application of the engineering adhesives
over the years,developed BD121 anti abrasion wearing resistant compound epoxy coating ceramic tile adhesives (product details from link:
http://www.wearcoating.com/abrasion%20resistant%20ceramic%20adhesive/wearing_ceramic_tile_bonding_repair_compound_epoxy_adhesive_4503.html),
suitable for the bonding of anti wearing abrasion resistant ceramic tile on the powder concentrator air inlet/air outlet.BD121 abrasion wearing resistant
compound epoxy coating ceramic adhesive is made from the toughening modified resin and special curing agent and other additives.High temperature
resistance,with good toughness and high strength,can cure at room temperature,the viscosity is moderate,in the process of the ceiling and facade
construction,not flowing,doesn't fall off.
Construction method:
At first,do the polishing,sand blasting and roughening treatment on the magnetic separator roller,to improve the bonding force.
Then wipe the bonding surface with solvent such as acetone or ethyl acetate etc,and dry it by airing for about 10 minutes,make the bonding surface be
dry and clean.
According to the specified ratio(A:B (mass ratio)=4:1),make the two components of the adhesives mix uniformly,then smear it on the bonding surface,
on the premise of ensuring no shortage of adhesives,the coatings are the thinner the better,had better smear the double-sided adhesives.Make the ceramic
tile after smearing the adhesives be folded and compacted with barrel.
It can be production after the adhesive curing for 24 hours,If you can heat it up to the temperature of 60 degree and keep this temperature for 2 hours,
then do the post curing,can get the higher comprehensive performance (can improve 30%).Every time the quantity of configuring adhesive should
not be too much,and the mixed-up adhesive should be used up before the coating time limit,in order to avoid causing waste.
Construction case photos of BD121 anti abrasion wearing resistant ceramic tile bonding repair epoxy adhesives:
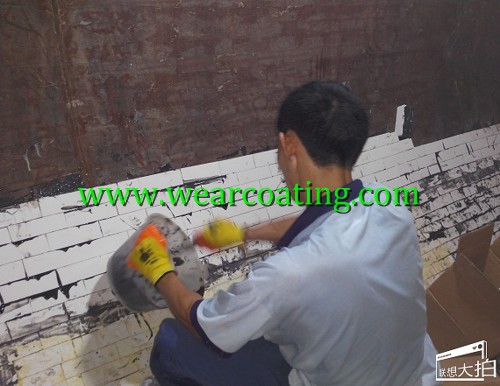
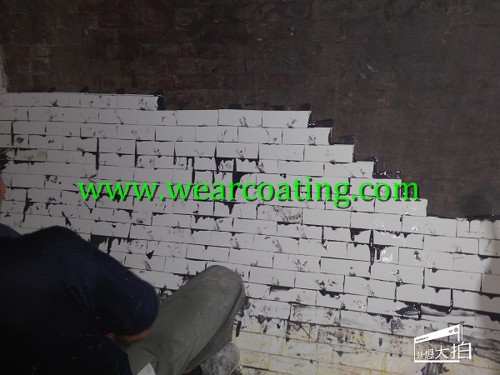
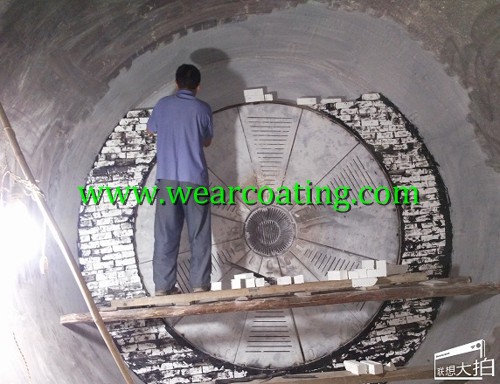
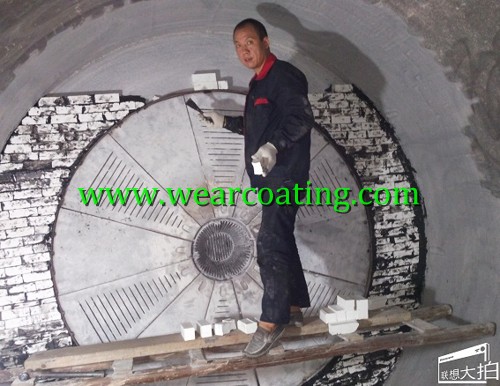
Product packaging actual photo of BD121 abrasion wearing resistant compound epoxy coating bonding ceramic tile adhesive:
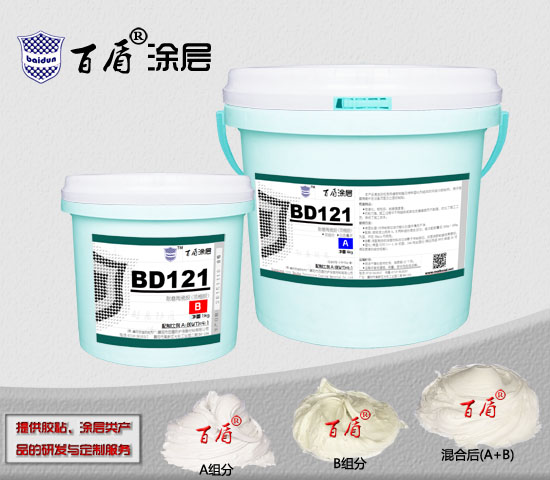