high temperature chemical impact wear abrasion corrosion resistant repairing and protecting
1.Clean up the rusting,dirt and other impurities on the surface of the substrate first,and do the sand blasting,polishing and coarsening treatment etc.
Clean it by cleaning agent and dry it by airing.Make the base material surface be clean,dry,no pollution and rough,to enhance the bonding strength
between coatings and the substrate.
2.According to the quality ratio A: B = 5:1,make the BD426 corrosion resistant coatings mix uniformly,smear it to the surface of the substrates uniformly,
the adhesive layers should be compacted,avoid appearing the holes,according to the criss cross method,smear a layer of coating on it for horizontal and
vertical,the thickness of each layer had better be 0.5-1mm.
3.After the second layer of the BD426 anti corrosion coating initial curing,make the BD408 flakes corrosion resistant coating mix uniformly according to
the quality ratio A: B = 4:1,make it be coating on the BD426 anti corrosive coating,the coating should be compacted along one direction to avoid
appearing the holes.Each layer thickness had better be 1-2mm.
4.After the BD408 flakes anti corrosion chemical resistant coating initial curing,make a layer of BD707 small particle wear resistant coating be
blade coating on its surface.The thickness is about 3mm.
5.After the BD707 small particles ceramic beads filling repair epoxy compound anti wear abrasion resistant coatings initial curing,make a layer of BD426
high temperature anti chemical corrosion resistant coatings brush coating on its surface as the topcoat.
6.After finishing smearing the abrasion resistant corrosion resistant coating,the coating will be complete curing after placing it for 24 hours
at room temperature.
Notes:
1.Each time the most quantity of configuring adhesives is not more than 2Kg,and used it up within 30 min for the mixed-up adhesives,
for fear of causing waste of adhesive curing.
2.must mix it uniformly when mixing it,the coating should be compacted when smearing it,avoid producing the bubble,cause it to produce holes
after the adhesive curing.At low temperature, can put A separate water bath heating components to reduce the viscosity, so that the rubber mixing.
3.When the temperature is below 15 degree,can heat it up to the temperature of 60-80 degree and keep this temperature for 2 hours after the coating
initial curing to promote the coatings complete curing.
Construction application case photos show:
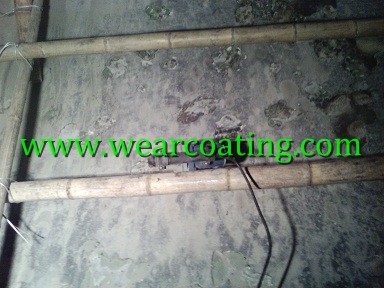
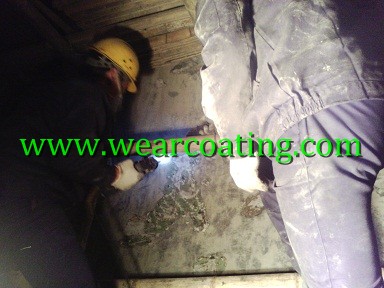

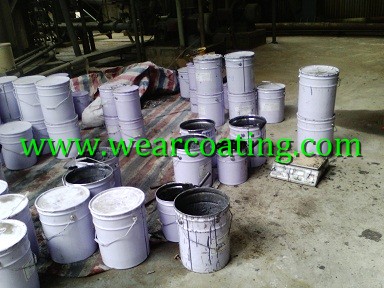