used in wet desulfurization system main equipment rubber lining pipeline repairing and protecting
1.The desulfurization of flue,the desulfurization of flue is divided into the original flue and clean flue.The temperature of original flue is high,
basically give priority to the abrasion wearing,smear the high temperature wear resistant coating materials for abrasion resistant protection,
this position and blower fan is the highest temperature parts of the desulfurization system,the wear resistant coatings should resist more than
160 degree temperature (dry) for a long time,at the same time,the coatings also have enough toughness,prevent it from causing cracking,
debonding between the coatings and metals or coating itself cracking when starting up and shutting down,the temperature changes fast.
This part combined coatings choose the BD427 high temperature anti chemical corrosion resistant coatings and BD776 high temperature wearing
abrasion impact resistant type silicon carbide coating,in this combination,mainly take advantage of the features of BD427 high bonding strength
as the primer transition layer,before the BD427 without curing,smear the BD776 on its surface,to make the wear resistant coatings achieve
the high strength bonding to the metals.
2.Net flue is the flue where the completed desulfurization flue gas passes through,the temperature was in 40 to 80 degree (wet),corrosion is the main
damage way,at the same time,there was also some wear and abrasion.This part combined protective coatings use the BD407 anti chemical abrasion
wearing corrosion resistant coating,BD408 high temperature flake anti corrosion wearing resistant compound ceramic epoxy coatings,BD7053
desulfurization absorption tower and slurry pipeline ceramic rubber lining pipeline repairing special anti chemical corrosion wear abrasion resistant coating.
We should use the BD407 for priming first during construction,and then smear the BD408 high temperature flake anti corrosion chemical resistant coatings,
finally smear the BD7053 desulfurization system equipment repair anti chemical corrosion abrasion wear resistant coatings to form the coating
structure of the inner corrosion resistant and the outer abrasion resistant.There is a large number of liquid rubber in the BD407,BD408 and BD7053,
on the one hand,can prevent penetration of water molecules to metal,on the other hand,can improve the toughness of the coatings to avoid the
coating itself cracking.
Construction case photos show for desulfuration system equipment repair anti wear abrasion corrosion resistant coatings:
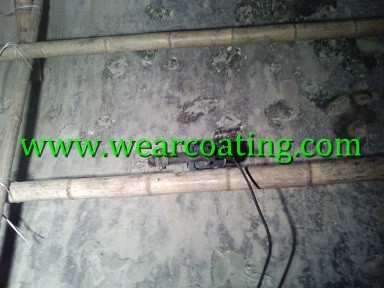
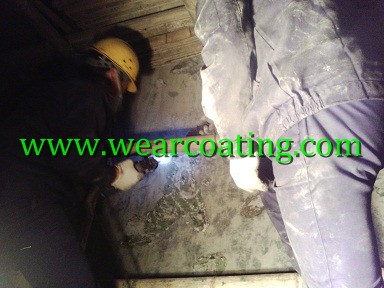
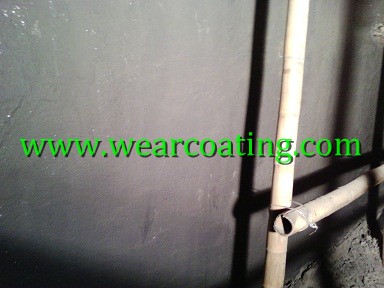
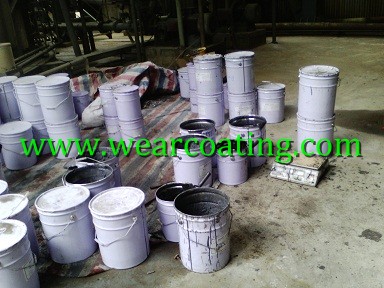